Quantum Sensor Improves Process and Quality Control by Analyzing Particles in Real Time
Stuttgart, 8th April 2024 -- The properties of raw materials and feedstock play a decisive role in analysis and production processes as well as in laboratory and process technology. Detailed information about the size, number, composition and distribution of particles contribute to process control and quality assurance. At Analytica in Munich, the Stuttgart-based high-tech start-up Q.ANT is showcasing a compact particle sensor for industrial applications that can be used to monitor these parameters in real time. The patented sensor, which is based on quantum technology, offers real added value for numerous sectors: from additive manufacturing, biotechnology, the ceramics industry, the materials and chemical industry to water treatment, medical technology and cosmetics.
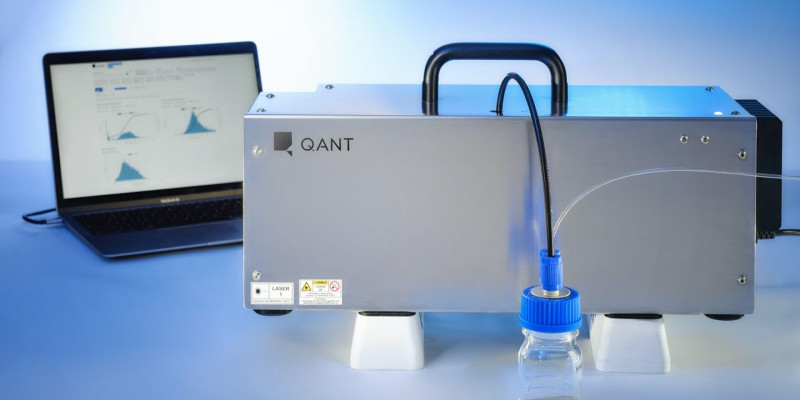
Accelerated shape detection without camera
Instead of taking samples and analyzing them in the laboratory, which is still standard in many industries, users receive immediate feedback on the quality and composition of ingredients. The sensor detects and analyses particles in raw materials and feedstocks, regardless of the medium, which can be liquid, gaseous or powdery. Process monitoring, process optimization and quality control are thus possible in real time. In addition to the size, number and distribution of individual particles, the sensor developed by Q.ANT will also be able to classify particle shapes in real time in the future. This is made possible by the quantum technology used in conjunction with an AI that can be trained to differentiate between predefined shapes, such as elliptical or spherical particles and round particles, which can also be used to identify agglomerates. For this purpose, the AI must be trained for specific “use cases”.
Numerous fields of application
There are many industries and fields of application for the particle sensor, which can also be used in combination with other measurement methods and mechanisms. For example, the quantum sensor can monitor algae cells in bioreactors and recognize dead cells as soon as they change their shape. The system control can then intervene to regulate the process without having to take samples from the reactor. Another example is water treatment: the AI recognizes contamination, for example by bacteria or other organisms that are difficult to detect, which allows conclusions to be drawn about the purification process. In additive manufacturing using 3D printing, as well as in the metal, ceramics and cement industries, the quantum sensor analyses different powder granulations, which can result in specific material properties. Other conceivable areas of application are the chemical and cosmetics industries, including pigment analysis for the development of colors and textures.
Q.ANT offers partnerships for specific applications
In order to develop specific applications, Q.ANT offers partnerships to interested companies. “We offer the industry early access to this new solution for particularly challenging problems without having to go through long development cycles,” says Vanessa Bader, Customer Project Engineer at Q.ANT. “Our partners have the opportunity to work with us to integrate the quantum sensor into their production processes and adapt it to their applications.” Q.ANT, which has patented the new technology, currently offers two particle sensors with different measuring ranges: from 2 to 50 micrometers and from 20 to 700 micrometers “With this range, we cover most applications in industrial production,” says Bader. Pilot projects indicate very high data quality. For example, the AI can distinguish particle agglomerates in metallic powders from individual particles that are just as large.
The compact sensor is easy to handle and quick to integrate
Another advantage: the compact quantum sensor fits on any laboratory bench and the system is quicker and easier to handle compared to the time-consuming conventional sampling process for analyzing particles. In addition to the laboratory device, feeding systems are being developed in the partner program to integrate the sensor inline into processes. A normal computer is all that is needed to transfer and visualize the measured data. The sensor is immediately ready for use via a website in the browser. “Nothing needs to be installed, you don’t need any extra computing power or complicated training for employees,” explains Bader.